Product Design vs. Industrial Design: Which One Does Your Business Need?
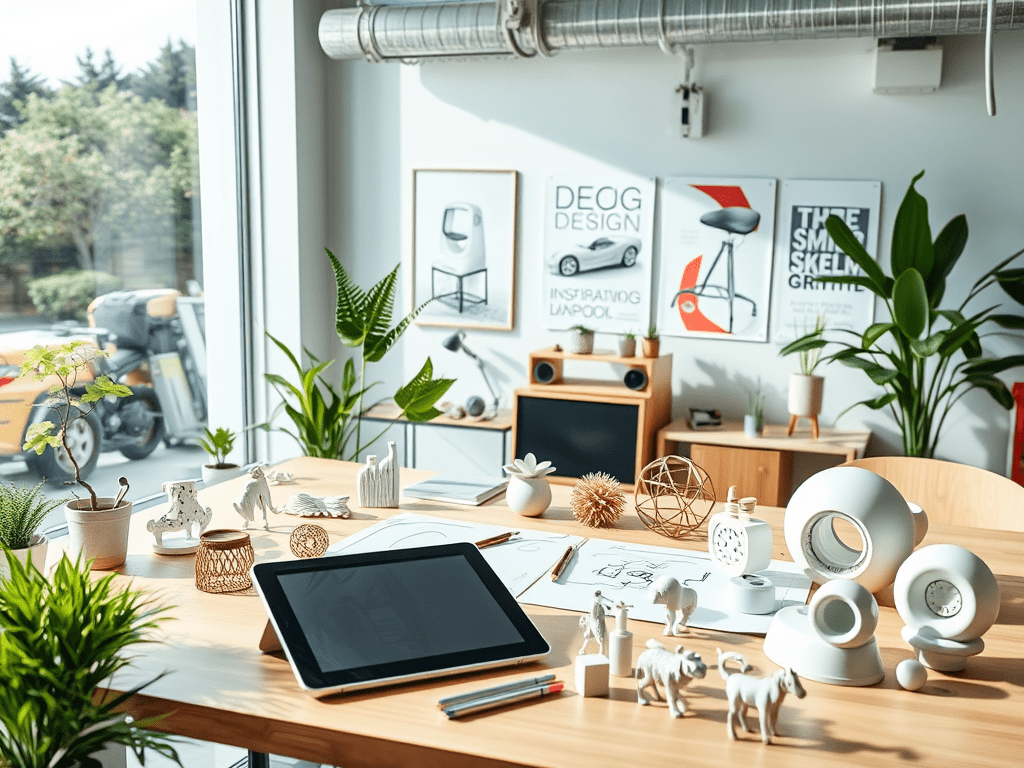
In today’s competitive market, effective design is crucial for business success. Two key disciplines – product design and industrial design – often create confusion among business owners and entrepreneurs. Let’s unpack these distinct yet complementary fields to help you make informed decisions for your business.
Understanding the Fundamentals
Product design and industrial design share a common goal: creating successful products that solve real problems. However, their approaches and focus areas differ significantly, impacting your business strategy and outcomes.
Product Design: The Digital-First Approach
Product design, especially in our digital age, emphasises the complete user experience. For eCommerce businesses and digital start-ups, this typically includes:
- User interface (UI) design for websites and apps
- Customer journey mapping
- Digital product development
- User experience (UX) optimisation
- Service design integration
For instance, if you run an online wellness store, product design focuses on creating an intuitive shopping experience, a seamless checkout process, and engaging digital touchpoints that reflect your brand values. A prime example from our portfolio is the Away Web App, which delivers a fully responsive platform for booking wellness experiences, ensuring a smooth user journey.
Industrial Design: Physical Product Excellence
In contrast, industrial design specialises in the development of physical products. This discipline is particularly relevant for businesses that:
- Manufacture physical products
- Need packaging solutions
- Require retail displays
- Want to create branded merchandise
- Plan to launch hardware products
A notable project that highlights our industrial design capabilities is Kabin Escapes, where we explored mindfulness accommodation design from concept to completion, focusing on creating physical spaces that resonate with their natural surroundings.
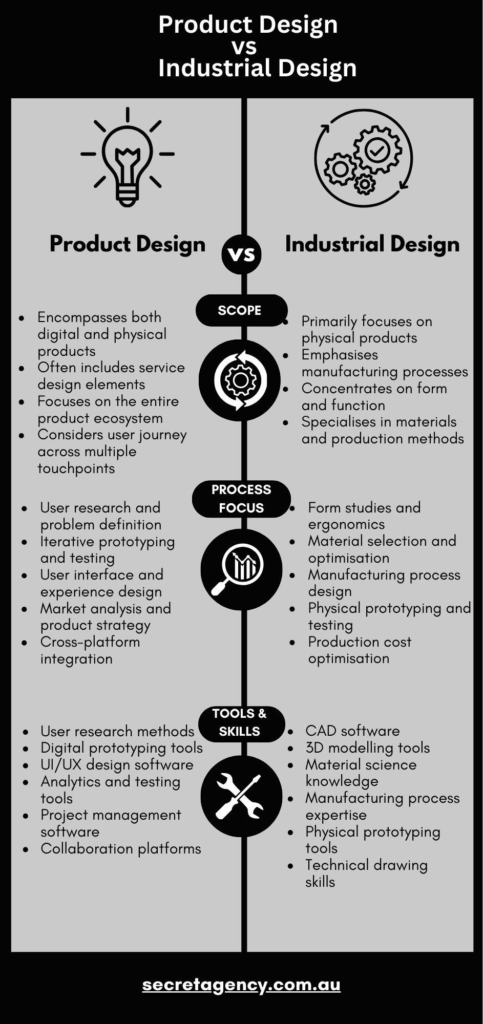
Different Approaches to Problem-Solving
Product Design Methodology
Product designers often start with extensive user research and problem definition. They ask questions like, “What problem are we solving?” and “How do users currently handle this challenge?” Their process typically involves:
- Conducting user interviews
- Creating user journey maps
- Developing digital prototypes
- Testing multiple iterations
- Refining based on user feedback
Industrial Design Methodology
Conversely, industrial designers begin with the physical constraints and possibilities. Their process often includes:
- Sketching and form studies
- Material selection
- Manufacturing process planning
- Physical prototyping
- Engineering collaboration
Tools of the Trade
Each field employs different tools to bring ideas to life. Product designers often utilise:
- Digital prototyping software
- User testing platforms
- Analytics tools
- Interface design software
Industrial designers typically work with:
- CAD software
- 3D printing technology
- Material testing equipment
- Physical modelling tools
The Overlap
While distinct, these disciplines often intersect in modern design practice. Consider a smart home device: product designers ensure the app interface is intuitive, while industrial designers focus on making the physical device both attractive and functional.
Choosing the Right Approach
The choice between product and industrial design often depends on your project’s needs:
- Creating a new app? Product design leads the way.
- Developing a physical gadget? Industrial design takes the helm.
- Working on a smart device? Both disciplines collaborate.
Conclusion: The Strategic Advantage
For businesses in Australia’s competitive market, understanding the distinction between product and industrial design is not just academic – it’s strategic. Whether you’re a start-up in Coffs Harbour or an established small business looking to scale, aligning your design strategy with your business goals can significantly impact your success.
As an award-winning creative agency since 2015, we’ve witnessed how the right design strategy can transform businesses. Whether you need product design for your digital presence or industrial design for physical products, the key lies in finding the right approach.
Ready to explore how design can transform your business? Let’s discuss your needs over coffee or a virtual chat. Our team of experienced professionals is here to guide you through the design journey that best suits your business objectives.
Book a free consultation to discuss your design needs with our expert team.